The intricate process of transforming plastic waste into usable fuel is a testament to the innovative strides in waste management technology. The mechanism driving plastic to fuel machines hinges on sophisticated methodologies, primarily pyrolysis, and catalytic depolymerization, each playing a pivotal role in the conversion process.
Pyrolysis: Unraveling Plastic Transformation
At the heart of plastic to fuel machine lies the concept of pyrolysis, an intricate thermal decomposition process. During pyrolysis, plastic polymers are subjected to intense heat in an oxygen-deprived environment, prompting the breakdown of long hydrocarbon chains into smaller molecules. This process occurs at temperatures typically ranging between 300°C to 800°C, a critical parameter optimizing the conversion efficiency.
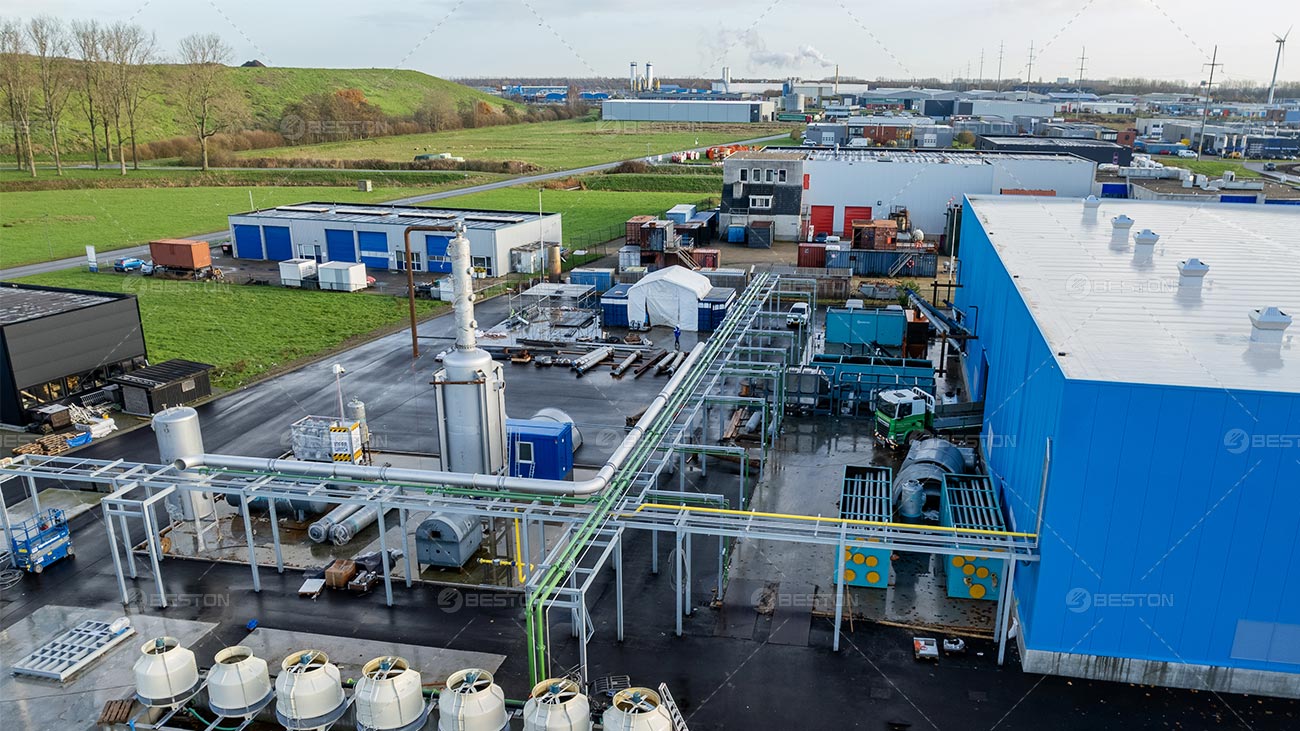
Catalytic Depolymerization: Augmenting Conversion Efficiency
Complementing pyrolysis, certain plastic to fuel machines employ catalytic depolymerization, which involves the use of catalysts to accelerate the breakdown of plastic molecules into simpler hydrocarbons. These catalysts facilitate the cleavage of chemical bonds within the plastic, refining the process and enhancing the yield of usable fuel products.
Feedstock Processing: Diverse Plastic Inputs
The plastic to oil plant showcase adaptability by accommodating a wide array of plastic inputs. From polyethylene (PE) to polypropylene (PP) and beyond, these machines effectively process various plastic types, mitigating the limitations associated with selective plastic recycling methods.
Thermal Decomposition and Product Yield
The thermal decomposition of plastics within plastic to fuel machines generates an array of outputs. This process yields valuable products like crude oil, hydrocarbon gases, and solid residues. The derived crude oil, a primary output, undergoes refining processes to obtain usable fuel products such as diesel, gasoline, or even aviation fuel.
Process Optimization and Environmental Considerations
Efforts in optimizing waste plastic pyrolysis plant revolve around maximizing conversion efficiency while minimizing environmental impact. Advanced technologies aim to fine-tune temperature control, pressure regulation, and residence time within the reactors, ensuring optimal conditions for the conversion process and reducing emissions of harmful byproducts.
Energy Recovery and Resource Utilization
The conversion of plastic waste into fuel via plastic to fuel machines presents a dual advantage. It not only addresses the burgeoning issue of plastic pollution but also harnesses the energy embedded within plastics, converting them into valuable fuel resources. This energy recovery aligns with sustainable practices, reducing reliance on traditional fossil fuels.
Innovations and Future Prospects
Continual advancements in plastic to fuel machine technology hold promise for the future. Ongoing research delves into improving reactor design, exploring novel catalysts, and integrating automation for enhanced operational efficiency. These innovations pave the way for more sustainable and economically viable waste management solutions.
In essence, the intricate fusion of pyrolysis, catalytic depolymerization, and sophisticated engineering defines the mechanism and technology behind plastic to fuel conversion. As these technologies evolve and gain traction, they stand as transformative solutions, addressing environmental concerns while unraveling opportunities for resource recovery and sustainable energy production. More information about Beston Group here.